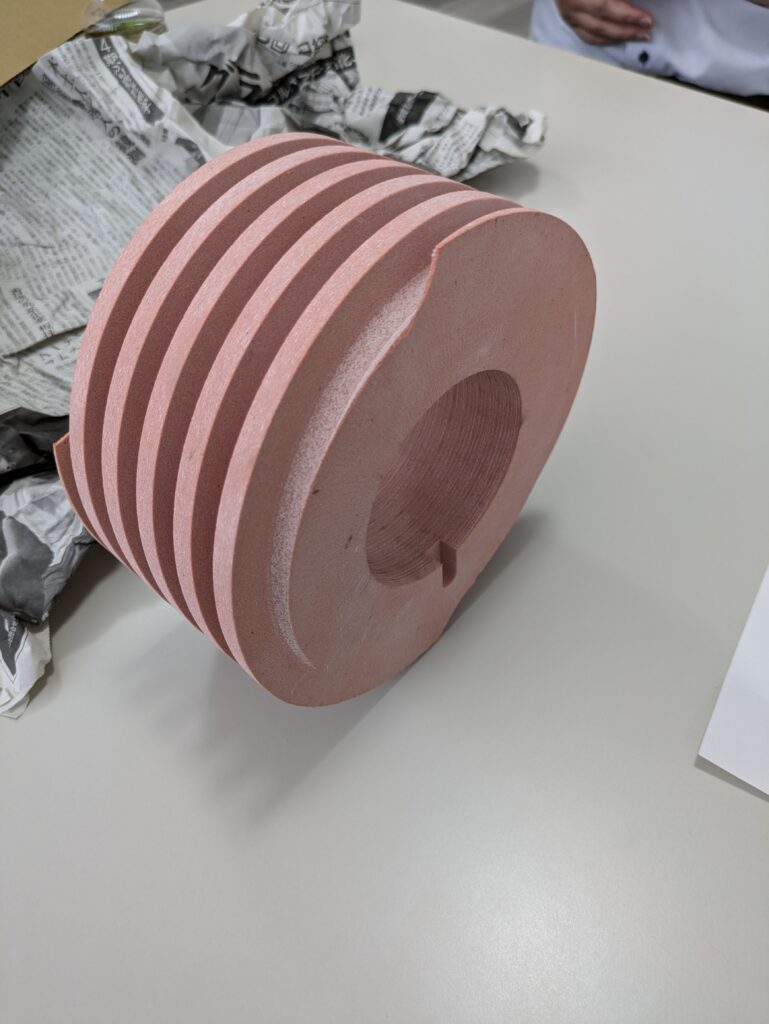
Since our establishment, we have been specializing in steel materials for cutting tools for three generations. We have accumulated expertise in all processes from raw materials to surface treatment. Currently, we also offer consultations on cutting tools such as steel materials for cutting tools and griding wheels / whetstones. There is a wonderful company called Disco, which started in the whetstone business with the same strengths of cutting, grinding, and polishing, and now manufactures processing equipment for semiconductor silicon wafers. What is the difference between Disco and Enserve? It’s the difference in the field. Disco focuses on the technology of “precisely cutting with whetstones”. We Enserve focus on the technology of “precisely cutting, grinding and polishing with metal materials”. We also understand whetstones, but that is to sharpen metal materials, not to cut with whetstones themselves.
Germany, England, and Japan are world famous for their cutlery. In Japan, we have been working on cutlery making, including Japanese swords, since ancient times, and we have unique whetstones and manufacturing methods that are different from those in England and Germany. So why does each country have different cutlery processing methods? This is because the principles are the same, but the way of thinking at the national and company level and the objects to be cut differ depending on the culture.
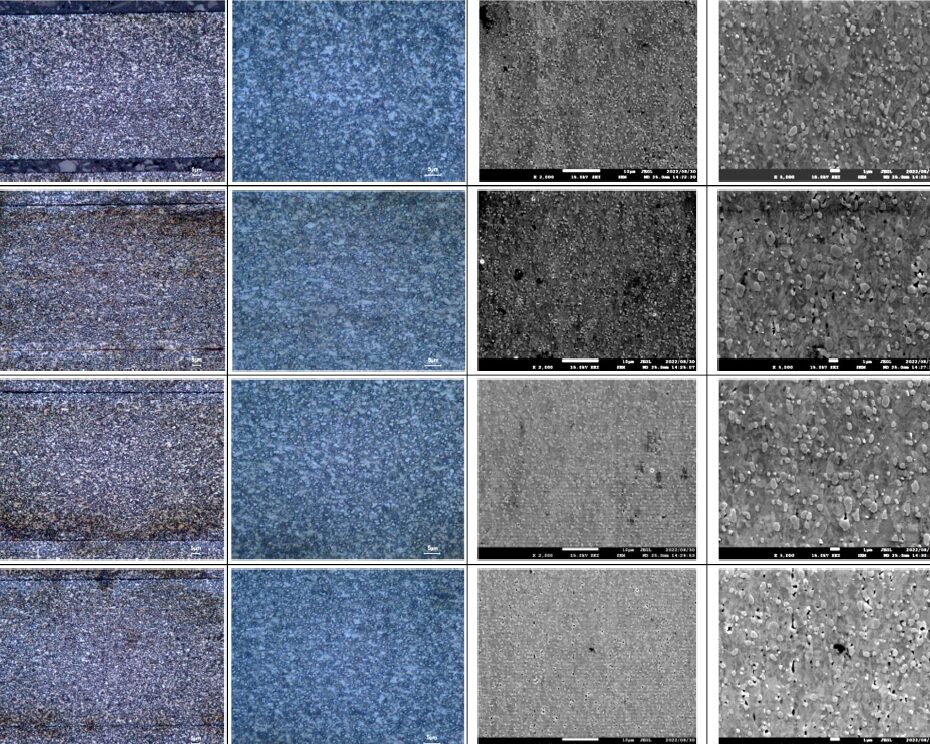
The world of cutting, grinding, and polishing is incredibly complex. Manufacturers worldwide constantly experiment and refine their techniques to achieve excellence.
Take blade materials, for example. Even with identical chemical compositions, variations occur in post-heat-treatment hardness and the speed at which the material hardens. Inconsistencies can also arise between manufacturing batches.
Why do these material discrepancies happen? Impurities, uneven distribution of elements, the mixing ratios of each chemical component, and the uniformity of carbide distribution and particle fineness all contribute. The knowledge of producing high-quality materials is the core expertise of steel mills.
Processing materials for blades, such as sharpening stones (whetstones) and surface treatments, also vary by country and the object being cut. Japanese razor blades, for instance, utilize exceptionally fine-grit griding wheels, resulting in incredibly sharp blades. In contrast, some overseas razors intentionally use slightly coarser grits griding wheels, prioritizing edge retention over extreme sharpness to maintain cutting performance for users with thicker beards.
Metal materials are essential for manufacturing in cutting and polishing industries. If you’re aiming for advanced techniques or facing material shortages, we assist in finding optimal solutions.
Enserve serves as your blade material development partner, providing expertise in materials, sharpening stones, and coatings. We connect you with global processing partners for tailored solutions. Even for domestic needs, we source alternative materials beyond your current suppliers.
When sourcing blade materials like special steel and martensitic stainless steel becomes challenging, we excel at finding them globally. We’ve consistently fueled our clients’ growth by securing these difficult-to-obtain materials.
To support your new material introductions, we offer comprehensive services from initial exploration and sample evaluation to thorough factory audits. Delegate your time-consuming procurement of blade metals, peripheral components (sharpening stones, sputtering targets), and equipment (blade processing and assembly machines) to us, so you can concentrate on your primary operations / development.
Below, we discuss the underlying material-related causes of common blade issues.