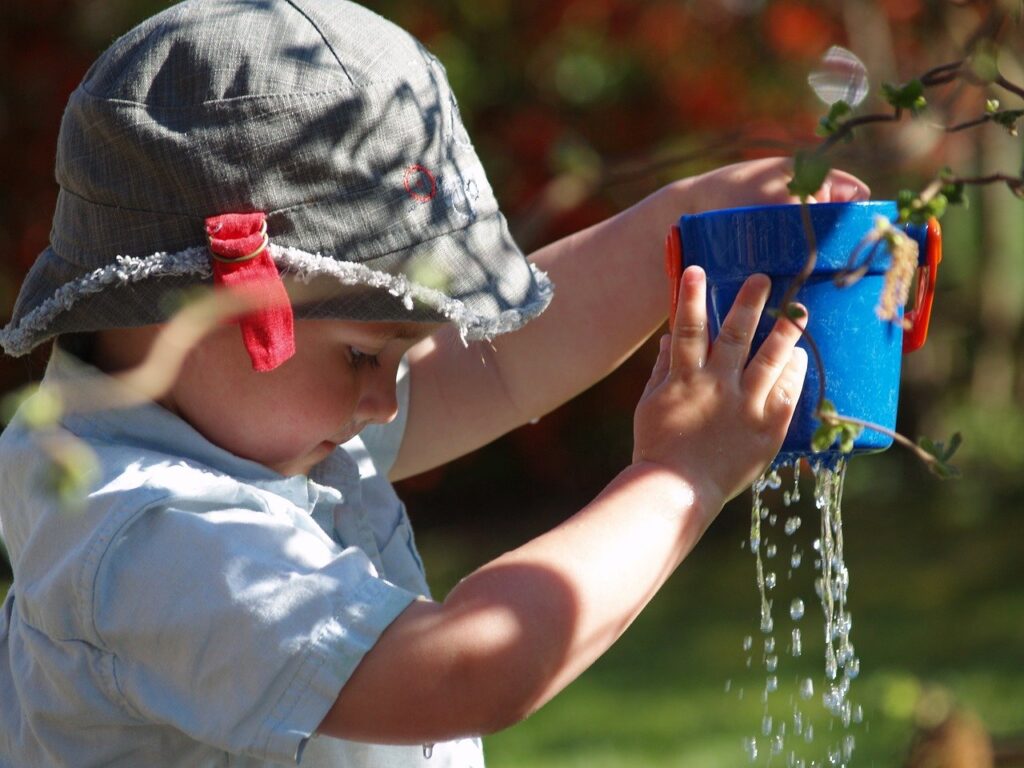
Are you experiencing quality issues with your current metal suppliers? Whether it’s non-conformances that fall outside of your supplier’s warranty or simply poor quality control, we can help.
Our team provides tailored solutions to address your specific quality challenges, including sourcing alternative materials that meet your exact specifications. We’ll work closely with you to ensure that you receive the highest quality components and avoid costly production delays and disruptions.
There are 3 typical issues of qualities for Metal materials or components.
Metal components that don’t meet your exact size / tolerance specifications can cause costly waste of materials / components, delays, and production stoppages. This is often caused by changes in processes due to lack of compliance with processing procedures, regular maintenance of equipment or tools.
Variations in metal composition can compromise the integrity and performance of your final product. These inconsistencies are caused by lack of impurity control inside the metal, variations in processing methods.
Scratches, dents, corrosions (specific article about corrosions) and other imperfections can impact the aesthetics and functionality of your product. These are caused by inadequate processing or insufficient protections.
For such quality issues, we offer the following solutions.
At we Enserve, we carefully listen to your issues first. We also identify your hidden / unspoken needs such as surface finish, burrs etc. Based on your issues, we make our own supply chains to solve your quality issues. In some cases, we even conduct the same shipping inspection as your acceptance inspection.
Managing relationships with manufacturers can be difficult due to differences in language, business practices, and culture. We have the know-how to prevent problems caused by cultural differences and to build good relationships with manufacturers in Asia, Europe, and the United States. You can leave us with your communication for manufacturing raw materials / components, and we will act as a good interpreter for your company to help you resolve quality issues.
You have your own quality philosophy and expectations. Enserve carefully aligns with these. To fully customize for your manufacturing process, we take a Step-by-Step Approach (a methodical approach to ensure quality control throughout each evaluation process – from a lab evaluation to mass production testing). We also plan to Risk Mitigation (strategies to minimize your business risks and safeguard your bottom line).
Enserve is a professional vendor in Tokyo specialized in Metals (Special Steel, Stainless, Copper Alloy) x Manufacturing (Industrial, Medical, Marine Petroleum). We establish tailor-made Supply Chain from all over the world to find your procurement solutions in the following areas.
We have the following product categories to assist your quality issues.
We have a case study how we carefully assist our customer for stable supply chain without sacrificing quality.